DfMA
What is Design for Manufacture and Assembly (DfMA)?
Design for Manufacture and Assembly (DfMA) is a way of designing and constructing a quality building more quickly, efficiently and sustainably.
Using a DfMA approach means that elements of a building are created in manufacturing environment rather than on site, and to more standard designs and specifications.
As a result, DfMA uses less energy and carbon and creates less waste. It is also safer.
Does BAM have expertise in DfMA?
Many of BAM’s projects include elements of DfMA and we have successfully adopted it in numerous sectors including education, commercial, industrial, leisure and health.
Earlier this year, BAM was appointed as an integrator and lead designer on the Construction Innovation Hubs platform program The two-year initiative brings industry together with academia to design and create a “kit of parts” which can be made by approved manufacturers and then used on public sector projects. Supported by the UK government the kit will meet their requirements in terms of safety, quality, whole life value, carbon and energy use.
Find out more about the construction innovation hubs platform program here.
To support our UK offering, our teams also access DFMA expertise from across Royal BAM Group where we have developed a number of market leading solutions. These include:
- Stroomversnelling a modular solution for retrofitting social housing in the Netherlands
- BAM modular which develops innovative elements for new build and retrofit residential projects
- MHI’s modular homes which are 80% constructed before they leave the factory
BAM is also developing new ways of delivering schemes both on and offsite. We have adopted the use of flying factories on constrained sites to keep disruption to a minimum and we have also established a 3D concrete printing factory in the Netherlands which prints concrete structures such as bridges, formwork, outlets and street furniture.
BAM is as an integrator and lead designer on the Construction
Innovation Hub’s platform programme. The two-year initiative will create
a manufactured kit of parts for use by the public sector on projects
and frameworks. BAM is one of eight contractors who will be working
collaboratively to design and manufacture the kit, in association with
the Manufacturing Technology Centre (MTC), BRE (Building Research
Establishment) and the Centre for Digital Built Britain (CDBB).
Participants
will develop and refine their products, technologies or services, which
will be installed and showcased on a proof-of-concept building.
Demonstrating how these solutions can be applied across a wide range of
UK government projects for vital new buildings like schools, hospitals
and prisons. The initiative is supported by the Government
Infrastructure and Project Authority and the kit will meet their
requirements in terms of safety, quality, whole life value, carbon and
energy use.
BAM has significant expertise in helping reduce the energy usage of houses or large buildings through retrofitting.
BAM
has successfully installed a "zero-on-the-meter" renovation on
thousands of social housing units in the Netherlands.
Known as Stroomversnelling, it improves comfort and reduces costs
for residents and reduces costs and carbon output for landlords.
Each
home is scanned using a 3D scanner and the data obtained is used to
design and manufacture a new façade
for the home in our own factory. By scanning each home, we ensure
that each new façade fits seamlessly onto the front of the property and
the same process is used to design and manufacture the roof elements and
solar panels. Currently we can
renovate two homes a day using this method.
BAM also installs
a heat pump with heat recovery and a new air handling unit in each
home. Turning each house fully electric and enabling it to generate its
own energy. We guarantee that the new
home will generate the predicted amount of energy and to assist with
this we monitor all resident’s energy consumption. BAM also has a
contract to maintain the homes for 40 years.
BAM has a controlling share in leading modular homes provider Modern
Homes Ireland (MHI) who constructs quality assured steel-framed
volumetric housing units and commercial buildings. These are
manufactured within a precision-controlled environment with units being
up-to 80% constructed before leaving the factory. This means that homes
can be constructed on site in just four weeks.
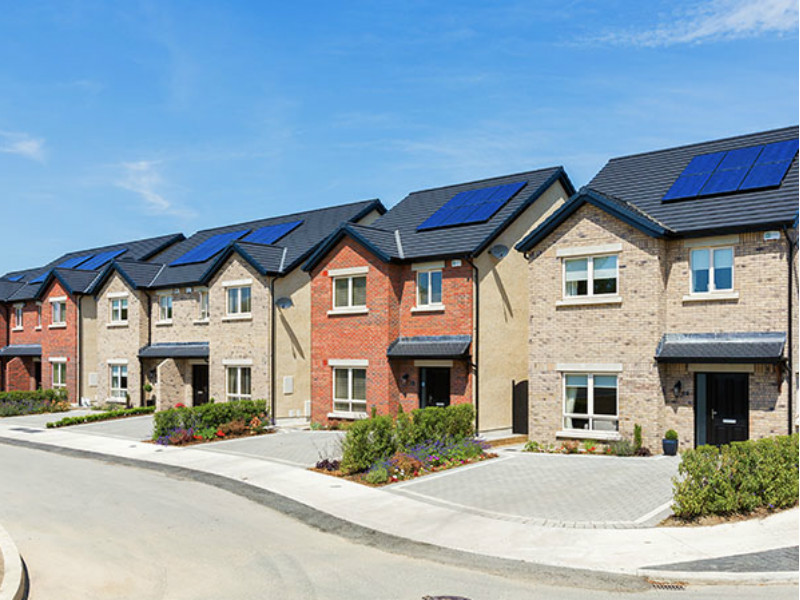
Zalmhaven is a new residential development in the heart of Rotterdam. The project was developed by Zalmhaven CV, a partnership of AM and investment manager Amvest. Zalmhaven consists of approximately 485 high-quality apartments, divided over a complex
of three towers: Zalmhaven I, II and III. Once complete, Zalmhaven I will be the highest residential building in the Benelux at 215 meters and will contain 256 apartments.
In order to build thehighest residential tower in Benelux, BAM has developed a hoisting
shed together with Civil Techniques de Boer. This factory is on four legs and provides a safe, working environment for our employees. As each floor is built the shed is lifted to enable us to construct the next.
The use of the shed and precast elements to construct the tower is enabling us to build one floor per week, cutting construction time from four years to three and a half.